Automatic Hinged Belt Filter
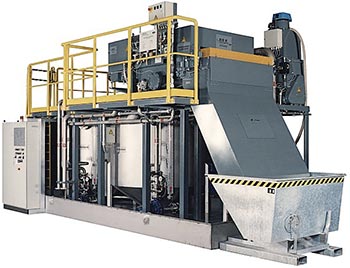
- BK 0.5 US/K – BK 2.5 US/K (0.5 – 2.5 m² filter area)
Dry cake discharge
No fleece consumption
compact systems are used for cleaning contaminated cutting fluids in metal processing and rolling mill operations. Cleaned cutting fluids have longer lifespan, improve the surface quality of workpieces or rolled goods, and help dissipate heat at the processing or forming location.
- Fully automatic operation
- Excellent filtration results without fleece consumption
- Minimal carryover of cutting fluid
- Dry cake discharge
- Low maintenance requirements
- Full-flow filtration
- Maximum lifespan of cutting fluid
- Option for emergency operation with fiber fleece
- The cleaned cutting fluid is supplied to the system pump (A) from the clean tank (B) of the processing machine (C). The contaminated cutting fluid is introduced into the dirt tank (E) of the folding belt filter system through the lifting stations. The internal processing of the system consists of two steps: “Filtration” and “Regeneration.”
Filtration:
At the start of filtration, the filter pump (F) is activated and delivers the contaminated cutting fluid from the dirt tank (E) through the filter inlet (G), passing through the folding belt filter (H) and the reusable (circulating) filter fabric (I), and then returns the cleaned cutting fluid to the clean tank (B) of the filter system through the filtrate outlet (J).
The dirt from the contaminated cutting fluid is retained on the filter fabric. As the filter fabric or cake becomes more clogged, the differential pressure in the folding belt filter (H) increases. The pressure is monitored by the attached contact pressure gauge (L) and triggers the regeneration of the fully automatic folding belt filter at an adjustable regeneration pressure. Even during the regeneration process, the processing machine is continuously supplied with cleaned cutting fluid.
Regeneration / Cake Drying:
After the regeneration is triggered by the contact pressure gauge (L) or the timer, the filter pump (F) is turned off, and the filter inlet (G) is closed. The upper chamber (M) of the folding belt filter is pressurized with compressed air, blowing in the filtration direction. The blown cutting fluid is returned to the system through the filtrate outlet (J), minimizing the carryover of cutting fluid.
Regeneration / Cake Discharge:
Once the cake drying process is complete, the upper chamber (M) of the folding belt filter is tilted upward using a pneumatic cylinder (N). Then, the belt drive motor (O) is activated, transporting the filter fabric (I) with the deposited cake to the cake discharge area. There, the cake is separated from the filter fabric using scrapers and peeling shaft (P). During the belt transport, the soiled section of the filter fabric is cleaned by a belt washing device and made available for a new filtration process. After the entire cake is discharged into the sludge container and the circulating filter fabric is cleaned, the upper chamber is closed, and a new filtration process begins with the refilling of the clean tank. Throughout the regeneration time, the processing machine is continuously supplied with cutting fluid from the clean tank.
Equipment (Example of a BK 1 US/K compact system with rectangular tank and lifting station):
The standard equipment of a compact system includes:
- Dirt tank (1) and clean tank (2) with adjustable level switches, walkable covers, and guardrails (3)
- Folding belt filter with circulating plastic fabric belt and the option for emergency operation with fiber fleece (4)
- System, filter, and flush pumps
- Compressed air monitoring
- Control cabinet with PLC and illuminated circuit diagram (7)
- On-site control elements on the folding belt filter (14)
- Mobile sludge bucket
- Execution according to operator-specific plant regulations
- Operation and maintenance manual
- Complete pneumatic and electrical installation
- Execution according to § 19.1 WHG (German Water Resources Act)
- CE marking
- Commissioning and operator training
Optional additional devices – Standard configuration:
- Immersion cooling unit or temperature control station (8)
- Cutting fluid mist extraction (9)
- Overflow valve or pump cascade control for supplying machine groups
- Platforms, ladders, or stairs (10)
- Lifting stations for low machine beds and ground-level installation (11)
- Automatic backup pump activation
- Fleece winding reel for fleece-sludge separation with “reel full” monitoring
- Skimmer devices for removal of non-emulsion oils
- Magnetic pre-separation for filter relief (12)
- Various maintenance levels during plant shutdown and weekend operation
- Maintenance contracts for preventive maintenance, as well as 24-hour delivery and repair service by experienced professionals
Optional additional equipment for operation as an “Anschwemmfilter-Klappbandfilteranlage” (swelling filter folding belt filter system):
- Fully automatic filter aid dosing device with capacitive low-level probe and loosening agitator (13)
- Dust-free bag emptying device for the filter aid dosing device to minimize excessive dust emission
- Makeup tank for the swelling medium
- “Umschaltkit” for implementing a dirty circuit before supplying the clean tank to optimize filtration quality
- Police filter in the system supply line
Fully automatic folding belt filter compact systems are used for the maintenance of cutting fluids of all kinds and achieve excellent filtration results without consuming fiber fleece. This results in a long lifespan of the cutting fluid and superior machining results with minimal operating costs.
They have proven themselves in various machining processes such as milling, drilling, turning, grinding, and fine grinding. The special design as a swelling filter folding belt filter also allows for use in fine grinding processes. Fully automatic compact systems are used to supply individual machines and machine groups, filtering the entire volume of cutting fluid in a full-flow manner. Standard configurations achieve filter areas of up to 2.5 m². In addition, pressure belt filter central systems are available.
Filter types based on filtration fineness and specific filter performance:
(Note: The specified flow rates are filter-specific basic performance values and serve as guidelines for interested operators.)
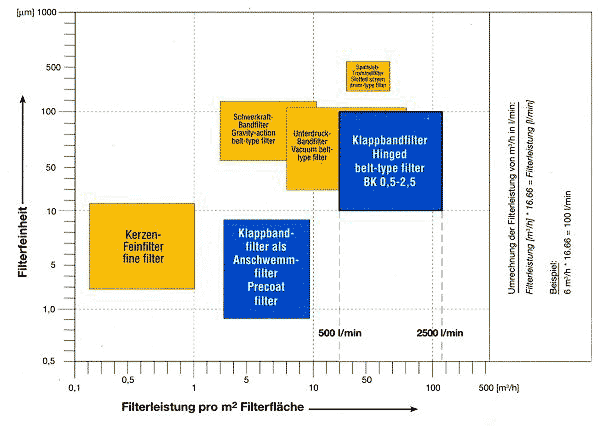
Our Service
Each filter system is specifically designed and customized for the specific application. We utilize our experience, in-house laboratory tests, as well as portable pilot plants for on-site testing at your company.