Vacuum Filter
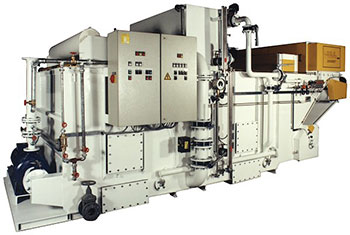
• BK 0.5 – 2.5 (0.5 – 2.5 m² filter area) U 0.25 – 40.0 (0.25 – 40.0 m² filter area)
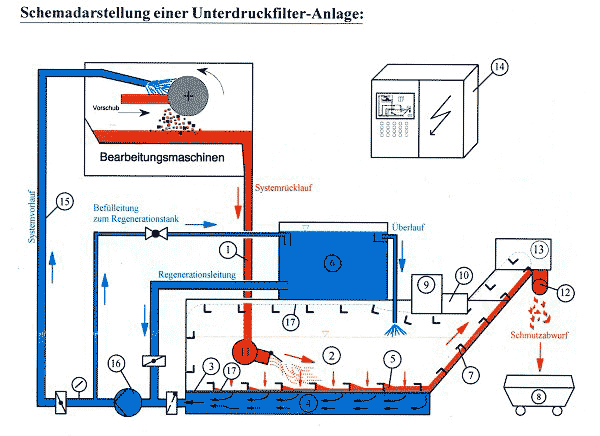
Vacuumfilters are used for the cleaning of contaminated cutting fluids in metal processing and rolling mill applications. Clean cutting fluids lead to longer tool life, improved surface quality of workpieces or rolled goods, and efficient heat dissipation at the processing or forming point.
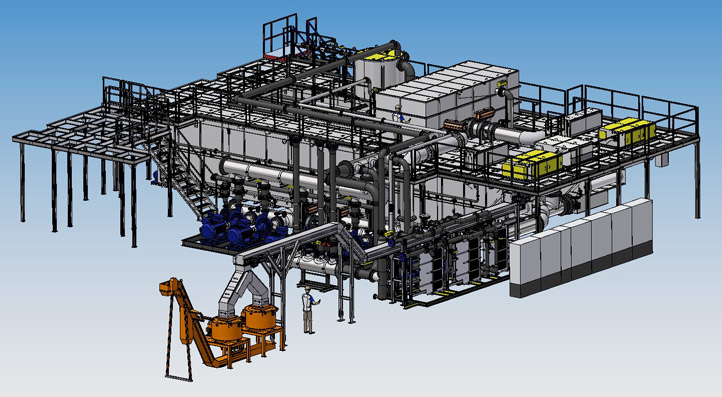
Advantages:
- Compact size
- Excellent filtration results
- Low installation effort
- Low maintenance requirements
- Affordable price
- Optional configuration without consumable filter fleece, with continuous filter belt, and washing device
- Significantly lower consumption of filter fleece compared to gravity filter systems during challenging filtration tasks and fleece operation
Operating Principle:
The contaminated cutting fluid flows through a piping system (1) and an inlet distributor (11) into the dirt chamber (2) of the underpressure filter tank. From the dirt chamber, the contaminated cutting fluid is suctioned by the filter/system pump (16) through the filter media (17) and the gap sieve (3) into the clean chamber (4). It is then pumped to the processing machines via the system supply line (15). Solid particles are retained, forming a filter cake (5) on the filter media.
As the filter cake builds up, the differential pressure in the lower chamber (4) of the underpressure filter increases. The filtration quality increases with increasing pressure. When an adjustable underpressure is exceeded, the filter regeneration is initiated. During regeneration, the machines are supplied from the regeneration tank (6) of the underpressure filter system, ensuring continuous machine operation.
During this phase, the scraper conveyor (7) is activated via the drive head (13) and the filter belt (17) is transported a small distance further. The dirt is then thrown into a container (8) via a discharge slope into the screw conveyor (12), the circulating filter belt (17) is cleaned in a washing device (10), tightened by the automatic tensioning device (9) and is thus cleaned and ready for use new filtration insert available. A new filtration cycle now begins, with the clean tank (6) being filled again.
The entire functional sequence is fully automatic and is controlled via a control cabinet (14) with an illuminated circuit diagram.
Equipment: The standard equipment of an underpressure filter includes:
• Container divided into dirt and clean chambers
• Regeneration tank
• Filter and system pumps
• accessible covers
• Baffle pot for pre-degassing
• Injector suction
• Switch cabinet
Optional additional devices:
• Pressure control station
• floating suction
• Skimmers
• circumferential filter belt
• Belt tensioning device
• Belt flushing device
• Lower chamber flushing
• Discharge screw
• Take-up reel for non-woven operation
• Oil mist extraction
Application: Underpressure filters are used both for supplying individual machines and supplying machine groups within centralized supply systems.
Available configurations:
- Compact filters for individual machine supply:
- U 0.25 K (0.25 m² filter area)
- U 0.5 K (0.5 m² filter area)
- U 0.75 K (0.75 m² filter area)
- U 1.0 K (1 m² filter area)
- Underpressure filters for supplying machine groups up to U 28 (28 m² filter area)
Example: Compact underpressure filter U 0.5 K supplying a grinding machine
U-0.5 K (Compact Filter):
- Filter area: 0.5 m²
- Flow rate: 120 l/min
- Medium: Oil/water emulsion
- Material: Steel
- Application: Grinding
- Design: Compact underpressure filter for supplying a grinding machine

U-0.5 K (Compact Filter):
Filterfläche: | 0,5 m² |
Volumenstrom: | 120 l/min |
Medium: | Ö/W-Emulsion |
Material: | Steel |
Bearbeitung: | Grinding |
Ausführung: | Compact underpressure filter for supplying a grinding machine |
Filter types based on filtration fineness and specific filter performance:
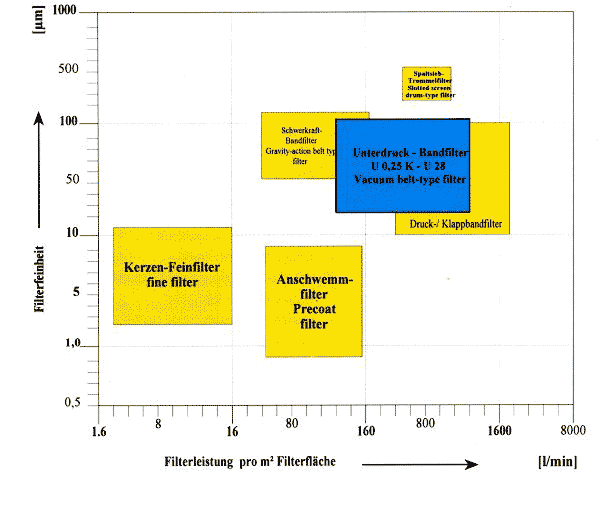
Our Service
Each filter system is specifically designed and customized for the specific application. We utilize our experience, in-house laboratory tests, as well as portable pilot plants for on-site testing at your company.