Pressure Belt Filter
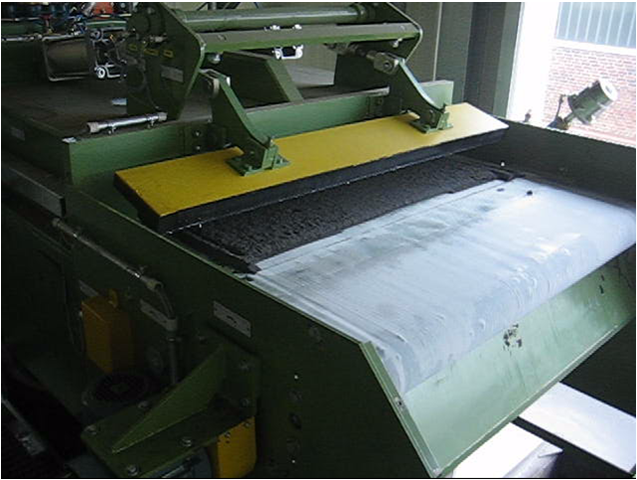
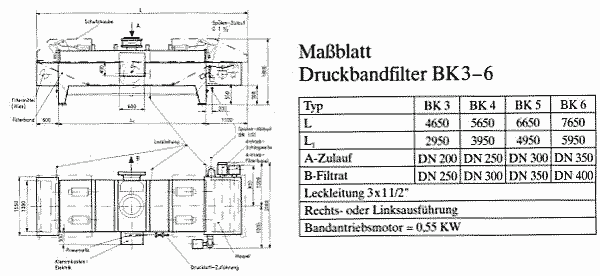
Pressure belt filters are used for cleaning contaminated cutting fluids in metal processing and rolling mill applications. Cleaned cutting fluids have longer lifespan, improve surface quality, and contribute to heat dissipation at the processing or forming point.
Advantages:
- High throughput capacity
- No backwashing during regeneration
- Easy discharge of filter cake
- Short regeneration time
- Compatible with various plastic filter belts
- High and low-pressure rinsing system
- Affordable price
Operation: The F.E.S. pressure belt filter addresses the need for filtration without disposal issues by utilizing a standard feature of a circulating plastic filter belt. A filter belt cleaning device is integrated into the head section of the belt filter. The closing mechanism of the sealing flaps, lowered pneumatic cylinders, and movable protective covers ensure a low height for easy installation and operation. The self-locking toggle lever mechanism keeps the chambers closed even in the event of an air pressure failure.
Equipment: The equipment of a pressure belt filter includes:
- Pneumatic control system
- Gap sieve filter belt support
- Circulating or reversing filter belt (optional)
- Rewinding reel for fleece usage (optional)
- Fleece roll holder (optional)
- Electrical control unit wiring in junction box
- Two-component DD-quality paint finish
Application: Pressure belt filters with filter areas ranging from 3 to 6 m² are primarily used in central cooling lubricant systems with high circulation rates.
The separation range, influenced by the formed filter cake, is between 10 and 100 µm. The nominal filter fineness of the filter fabric used also affects the initial filtrate after a filter regeneration. The basic filter performance is 1,500 l/min per m² of filter area.
The viscosity of the cutting fluid, the workpiece material, and the machining process impact the throughput capacity. The actual filter performance ranges between 500 and 2,500 l/min per m² of filter area.
By adding filter aids such as diatomaceous earth or cellulose, the filter can also be used as a precoat filter for challenging filtration applications.
Filter types based on filter fineness and specific filter performance:
The specified throughput capacities represent basic filter performance and serve as guidelines for interested operators.
Please note that the information provided is a translation, and for accurate details and further assistance, it is recommended to consult F.E.S. directly.
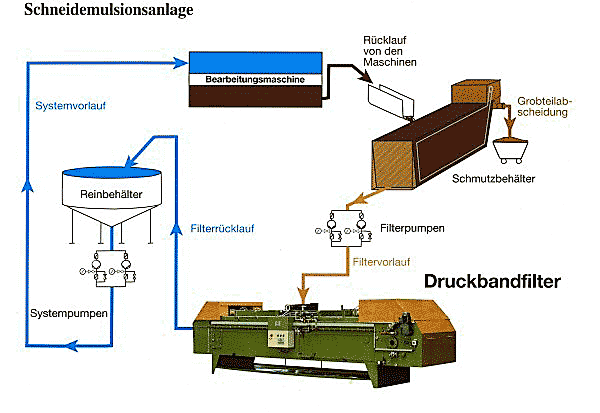
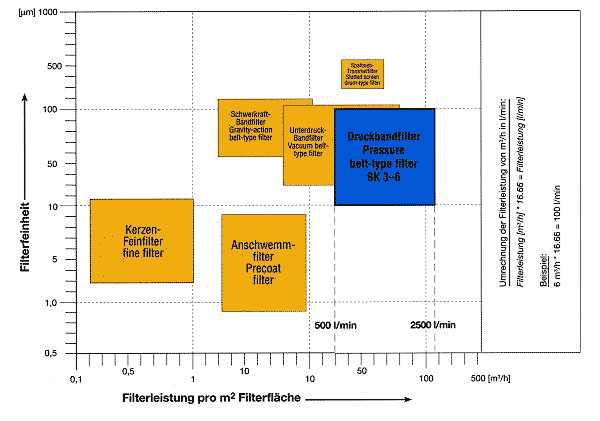
Our Service
Each filter system is specifically designed and customized for the specific application. We utilize our experience, in-house laboratory tests, as well as portable pilot plants for on-site testing at your company.